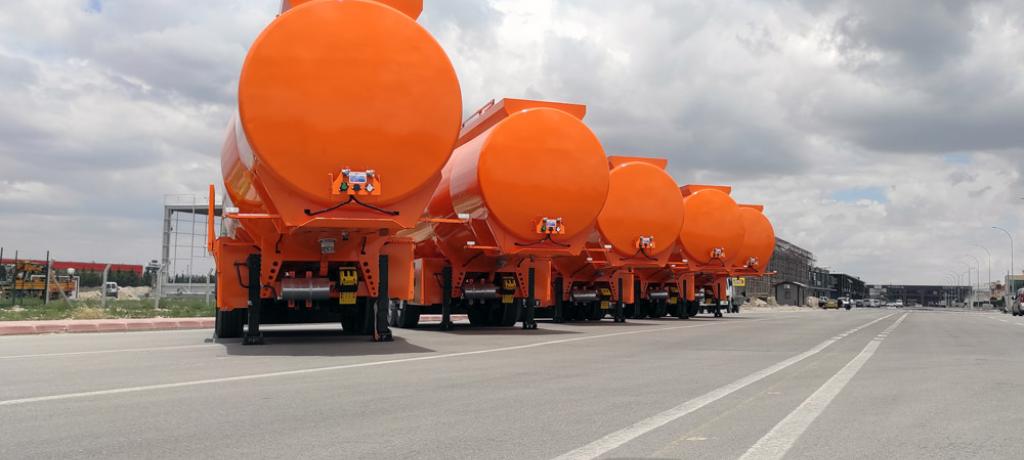
LNG market trends in energy and execution efficiency
LNG: The drive for efficiency in increasingly challenging times
Providing reliable, affordable energy to support prosperity and enhance living standards is coupled with the need to do so in ways that reduce impacts on the environment, including the risks of climate change. This is society’s dual challenge and MAS Trailer takes it seriously.
For over 60 years, the LNG Industry has demonstrated and delivered innovation in the delivery of natural gas. The ultimate goal looks to achieve the lowest cost of supply to produce LNG. Two big levers are (1) energy efficiency in operations, and (2) capital cost and execution efficiency. Competitive LNG market trends calls for pulling both levers so that natural gas and LNG can continue to be part of the solution to the Dual Energy Challenge.
LNG: Trends in energy and execution efficiency
Trends in energy efficiency
Liquefaction of natural gas (LNG) is a highly energy intensive process driven primarily by large refrigeration requirements. Much effort has been applied to increase LNG process efficiency with choices of process components & refrigeration compression drivers. In addition, the industry has also concentrated on how to design and deploy LNG technology for “execution efficiency.” No stone of the LNG value chain is left unturned.
Ultimately LNG competes as a commodity so overall “cost of supply” (COS) is critical to the market share that LNG can obtain and sustain.
Among the technical dimensions considered in designing an LNG liquefaction plant are:
LNG process efficiency as measured by “specific power,” i.e. the power needed to produce each unit of LNG [1].
Availability, as the percentage of the year a plant can produce LNG. Availability is largely driven by the choice of refrigeration compressor drivers & their maintenance cycle.
Capital cost for a unit of production, for example, “capital cost per ton of LNG produced per annum” often expressed as “$ / ton.”
Complementary and symbiotic to the significant innovation in LNG processing is innovation in turbomachinery over the decades. Turbomachinery innovation over this period enabled the growth of LNG plant capacity by enabling more refrigeration capacity from fewer refrigeration compressors. The incentive was perceived to be achieving more process simplicity and “economy of scale” in capital costs.
Turbomachinery used to power the refrigeration that liquefies natural gas has an even longer history of innovation. LNG refrigeration drivers started with steam turbines but soon migrated to gas turbines in order to grow refrigeration and LNG capacity by leveraging improvements from the aviation and power generation sectors. The gas turbine, the workhorse of LNG refrigeration drivers, has risen in fuel efficiency from ~17% to over 40% in ~80 years [2] [3].
That increase in energy efficiency is for a “simple cycle” where the gas turbine is used to directly drive liquefaction refrigeration compressors and or electric generators without further exhaust stack waste heat recovery. Ivan G. Rice tells a fascinating history of the people involved in the development of gas turbines in “combined-cycle” use [4][5]. Combined cycle adds heat recovery from the hot gas turbine exhaust to generate steam which then drives a steam turbine on other turbomachinery. Gas turbine manufacturers have achieved 62% to 64% net efficiency [6][7] on their newest “combined cycle” power plants.
LNG train capacity grew with the development of gas turbines. Gas turbine ‘strings’ were then supplemented using large electric “helper motors” coupled to gas turbines on the same driveline to provide more power for the refrigeration compressors. This increasing refrigeration power in each LNG Train can be described as “power density.”
Another variation on refrigeration drivers can be seen with two baseload LNG plants which exclusively use large electric motors to power baseload production of “all-electric LNG.” The prize of “all electric LNG” is higher annual availability & LNG production because gas turbine scheduled maintenance is removed from directly impacting LNG production. Conventional wisdom has been that “all-electric LNG” came at a higher capital investment. Technology is available to be more energy efficient in LNG production. It would be nice if such energy efficiency could be realized without a capital investment increase which directionally offsets energy efficiency in the total LNG cost of supply.